Bloczki betonowe: rodzaje, cechy i proces samoprodukcji
Jednym z najczęstszych materiałów do budowy ścian nośnych i ścianek działowych budynków mieszkalnych, a także małych budynków przemysłowych są bloczki betonowe. Ich popularność wynika z niskich kosztów, doskonałej wydajności i dużej liczby odmian, co pozwala wybrać odpowiednią jednostkę do prawie każdego zadania.
Instrukcje zawarte w tym artykule pomogą ci nauczyć się samemu tworzyć bloki betonowe, a także zapoznać się z ich istniejącymi typami.

Odmiany sztucznych kamieni betonowych
Zastanów się nad głównymi typami + charakterystyką budowania bloków betonowych, które są najczęściej stosowane w nowoczesnym budownictwie.
Shlakoblok
Te kamienie ścienne wykonane są metodą betonowania wibroprasowanego na specjalnych platformach.
Skład mieszaniny, z której wykonany jest blok żużlowy, może obejmować:
- kruszony kamień do wyrobów betonowych;
- bitwa z cegły;
- trociny;
- keramzit.
Właściwości techniczne bloków betonowych z żużlem pozostawiają wiele do życzenia, ale ze względu na fakt, że ich cena jest jedną z najniższych na rynku, blok żużlowy jest szeroko stosowany w budownictwie indywidualnym.
Ale koszt jest chyba jedyną zaletą, ponieważ pozostają w tyle za innymi materiałami w następujących parametrach:
- wytrzymałość;
- parametry oszczędzania ciepła;
- siła.
Głównym zakresem bloków są małe budynki, które nie będą poddawane dużym obciążeniom:
- szopy;
- garaże;
- letnie kuchnie;
- warsztaty i tak dalej.
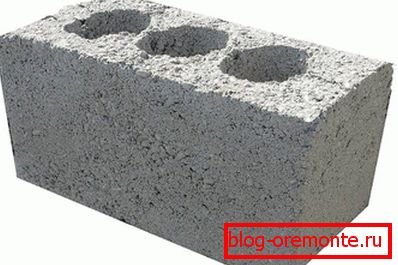
Arbolit
Mniej powszechny materiał, który składa się z następujących elementów:
- materia organiczna (głównie drewno);
- element wiążący (proszek);
- utwardzacz.
W rzeczywistości ten sztuczny kamień składa się z trocin zamkniętych w betonowej skorupie.
Zalety materiału są oczywiste:
- mała waga bloku betonowego;
- wysokie właściwości termoizolacyjne;
- dobra izolacja akustyczna;
- skuteczna wymiana powietrza.
Aby chronić bloki przed negatywnymi skutkami środowiska, kamienie są traktowane za pomocą specjalnego rozwiązania. Zapobiega to tworzeniu się pleśni i zapobiega gniciu.
Beton z drewna jest idealny do budowy małych domów, które nadają się do całorocznego życia bez użycia dodatkowej izolacji.
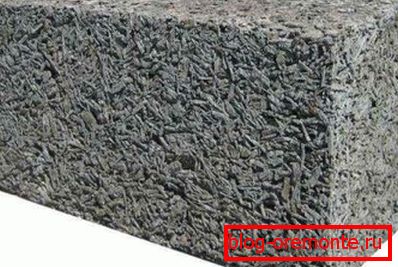
Bloki i bloki pontonowe
Bloczki z betonu komórkowego według GOST, które określają ich charakterystykę techniczną, powinny składać się ze sztucznie wytworzonych porów (komórek) wypełnionych powietrzem o 70-85%. Najczęstsze bloki pianki i gazu.
Te materiały mają następujące zalety:
- są lekkie, w wyniku czego transport kostek betonowych i ich instalacja w prywatnej zabudowie nie wymaga użycia specjalnego sprzętu;
- łatwa obsługa - możesz nadać niezbędny kształt jednostce komórkowej za pomocą zwykłej piły do drewna;
- ściany z bloczków z betonu komórkowego dobrze utrzymują ciepło i mają doskonałe właściwości izolacyjne.
Bloki betonu o strukturze komórkowej wykonane są z roztworu zawierającego piasek, cement i kruszywo. Do pianki dodaje się wapno, proszek aluminiowy lub inny spieniacz.
Zwróć uwagę! W przeciwieństwie do pianobetonu, beton komórkowy poddawany jest dodatkowej obróbce w piecu autoklawowym, gdzie jest poddawany działaniu wysokiej temperatury pod wysokim ciśnieniem (10-12 MPa). W rezultacie materiał ten nabiera większej siły: prawie nie można go zmiażdżyć ani złamać.

Niezależna produkcja bloków
Technologia produkcji sztucznego kamienia z zaprawy cementowej z wypełniaczem jest stosunkowo prosta, co pozwala na samodzielne wykonywanie bloków betonowych.
Prace przygotowawcze
Na początkowym etapie konieczne jest określenie wielkości przyszłego bloku. W przypadku produkcji niezależnej parametry każdego pojedynczego elementu są ustalane na podstawie wymaganej szerokości ściany.
Grubość dna bloku nie powinna być mniejsza niż 2 cm, a ściany pustek nie powinny być mniejsze niż 4 cm, w tym przypadku standardowy kamień o wymiarach 20x20x40 cm z pustkami wewnątrz waży około 40 kg, co czyni go wygodnym do murowania.
Do produkcji potrzebny będzie każdy płaski grunt, pokryty folią i specjalnymi formami bez dna.
Materiał dla formularzy będzie:
- deski;
- DSP;
- sklejka
Aby chronić drzewo przed uszkodzeniem, wnętrze formy jest osłonięte blachą. Wkładki są wykonane w podobny sposób, dzięki czemu pustki powstają w gotowym bloku. Poprawiają właściwości izolacyjne materiału i ułatwiają go.

Bloki betonowe własnymi rękami mogą być wykonane szybciej, jeśli wykonasz kilka form w jednym bloku. To wymaga sklejki lub szerokości deski równej wysokości przyszłego bloku. Materiał jest cięty na kawałki i mocowany za pomocą śrub. Tworzone są dalsze wewnętrzne partycje.
Wskazówka! Aby zamrożony blok mógł być łatwo oddzielony od formy, wszystkie jego części muszą zostać nasmarowane nafty, smaru lub płynu niezamarzającego.
Proces produkcyjny
Do odlewania bloczków betonowych potrzebne będą następujące materiały:
- żwir o drobnej frakcji;
- cement;
- piasek;
- woda;
- wapno;
- drut do zbrojenia.
Liczba każdego składnika jest określana na podstawie twoich potrzeb dotyczących sztucznego kamienia. Proporcje cementu, piasku i żwiru są przyjmowane w stosunku 1: 3: 5.

Dla wygody podzielimy cały następny proces na kilka etapów.
- Żwir, piasek i cement należy umieścić w mieszalniku.. Następnie w procesie mieszania małymi porcjami dodajemy wapno. Na ostatnim etapie mieszania dodaje się wodę. Gotowy roztwór nie powinien być zbyt płynny, aby nie wypłynął z formy. W końcu dostajesz konkretną markę M135 wypełnioną drobnym żwirem.
- Mieszanka betonowych betonowisk ułożona w postaci warstwy o grubości 2 cm. Po tym, wkładki są ustalone, które są niezbędne do tworzenia pustek wewnątrz sztucznego kamienia. Możliwe jest mocowanie płytek za pomocą poprzecznych szyn, które są usuwane po wypełnieniu jedną trzecią formy betonem.
- Dno formularza powinno być pokryte gazetami lub papierem.. Zapobiegnie to przywieraniu betonu do podstawy. Mieszanina wypełniająca formularz musi być półwytrawna. Sprawdza się to w ten sposób: biorąc małe rozwiązanie, należy je zmiażdżyć i położyć na płaskiej powierzchni. Bryła powinna zachowywać swój kształt, nie rozprzestrzeniać się.
- Po wypełnieniu formy do połowy wysokości, należy ułożyć zbrojenie, które uczyni przyszły kamień bardziej wytrzymałym..
- Zamiast wkładek można używać pustych butelek do tworzenia pustych przestrzeni wewnątrz bloku betonowego.. Zamyka się korkiem i zamurowuje w kamieniu.
- Po ostatecznym napełnieniu formy, zaprawę należy zagęścić i wyrównać za pomocą kielni..
- Możliwe jest wyjęcie bloków z formularzy na 4-5 dni, ale można je stosować w pracy dopiero po 2-3 tygodniach, gdy tylko roztwór stwardnieje.
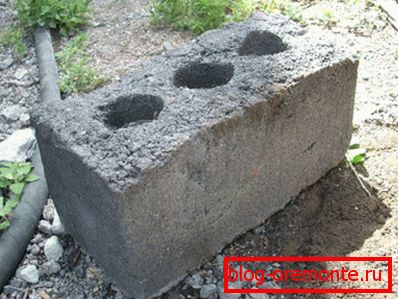
Wniosek
Opisana powyżej technologia pozwala bez wysiłku wykonywać betonowe bloki własnymi rękami. Charakterystyka techniczna gotowych produktów nie będzie w żaden sposób gorsza od ich odpowiedników, sprzedawanych w supermarketach budowlanych, a rozmiar idealnie pasuje do Twoich potrzeb. Ponadto możliwe jest znaczne obniżenie kosztów zakupu materiałów budowlanych i ich dostawy.
Więcej informacji na temat materiału pomoże wideo w tym artykule.